Manufacturing Problems That Impact Competitive Advantage
Manufacturing has always been an industry driven by rapid change. Advances in technology—such as artificial intelligence and automation—fuel the never-ending race for efficiency in manufacturing. Shifts in customer expectations raise the bar for volume, speed and quality of experience. As a result of increasing globalization, emerging competitors might have the advantage of cheaper skilled labor, better local infrastructure, less restrictive regulations or simply a local connection to a desirable customer base.
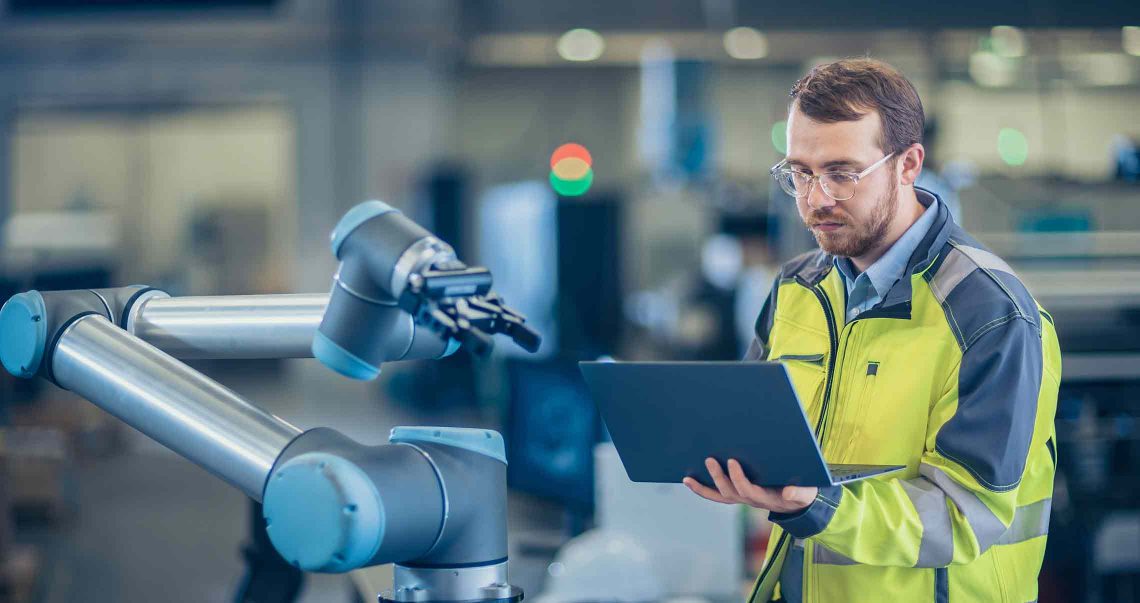
To thrive, companies must tackle common manufacturing problems impacting their ability to maintain a competitive advantage. Digital solutions have an important role to play in this effort, helping companies generate greater customer loyalty, push for increased profitability and drive market share.
Digital transformation and automation
To increase efficiency, manufacturers are using digital technologies to create or modify existing business processes. Digital transformation and automation can be an opportunity to pursue real value. You can cut costs while maintaining or improving quality and strengthening relationships with producers, suppliers and customers. Modifying your procedures can also help you respond with more agility to shifts in customer demand or supply chain, identify and penetrate new markets faster, and improve internal workplace culture.
Even better, digital transformation is scalable. Small, manageable steps—such as automating data collection—can garner big wins by enabling real-time, insight-based decision-making.
Data collection and storage can be cheap and flexible. Predictive analytics and artificial intelligence have also become more accessible. These technologies allow manufacturers of all sizes to draw insights from large amounts of data. Using internet-connected devices, your systems can gather meaningful data 24/7 across the value chain without the need for additional labor. Information about customer experience, plant energy consumption, equipment utilization and raw materials can increase overall performance while reducing costs.
Addressing cybersecurity
As these technologies have grown more widespread in the industry, cybersecurity has made its way to the top of the list of manufacturing challenges. Global estimates by IBM state that in 2023, data breaches cost an average of $4.45 million globally. All business information is an asset, and potential cyberattackers can target a range of information, including:
- Product blueprints and other intellectual property
- Internal financial information
- Supplier contacts and transactions
- Customer financial data
- Plant, equipment and operational data
If you don't think your company won't be a likely target, think again. Due to the way common cyberweapons such as ransomware and malware can spread, your business could become collateral damage in attacks on customers or vendors in the supply chain. Manufacturers who choose to ignore cybersecurity risks may find themselves falling behind the competition. Data theft can cause financial losses but also legal, compliance and reputational damage.
According to the National Association of Manufacturers Manufacturing in 2030 Survey, only about 2/3 of manufacturers have a formal or a partial policy on data quality. To stay on top of the threats, invest in IT staff or consultants that specialize in cybersecurity. Work closely with these experts to develop a robust prevention and recovery plan. Honest human errors can often play a role in breaches. Train all staff in prevention and mitigation measures that are relevant to their roles and tasks. It's a good idea to keep offline contingency plans in place in the event of major software outages.
Finding the right team
Competition for talent is a top concern in manufacturing. In 2024, there are about 600,000 unfilled manufacturing jobs in the US. This total is expected to reach 2.1 million by 2030, according to a recent study by Deloitte and the Manufacturing Institute. The study also found that 83% of surveyed manufacturers cited attracting and retaining talent as their top challenge.
Two key drivers of this challenge are the aging workforce and the skills gap. Today's employees need to be proficient in several high-technology skill areas. As baby boomers continue to retire over the next decade, attracting multi-skilled labor will be increasingly difficult. Your ideal candidate—whether fresh from school or hailing from another industry—may carry limited perceptions about the nature of the work, growth opportunities and pay available in manufacturing careers.
It's up to you to engage new talent with strategic recruiting tactics. Look outside of manufacturing for candidates with elite but transferable skills. These might include hydraulics, robotics, electrical engineering, laboratory techniques and computer science. Create bridge programs, such as paid on-the-job training for new and experienced workers. Invest in diversity and inclusion initiatives so workers from traditionally underrepresented backgrounds can see your company as a welcoming workplace.
The bottom line
Manufacturing is a field in transition, with new technologies changing the way operations are handled and increasing competition across the industry. By investing in the right areas, your business can stay a step ahead and tackle some of the emerging manufacturing problems of this new era without falling behind the pack.