Risk management in manufacturing best practices
For manufacturers, increased globalization and advancing technology offer new opportunities. But these changes can also be disruptive, bringing new potential risks along with them.
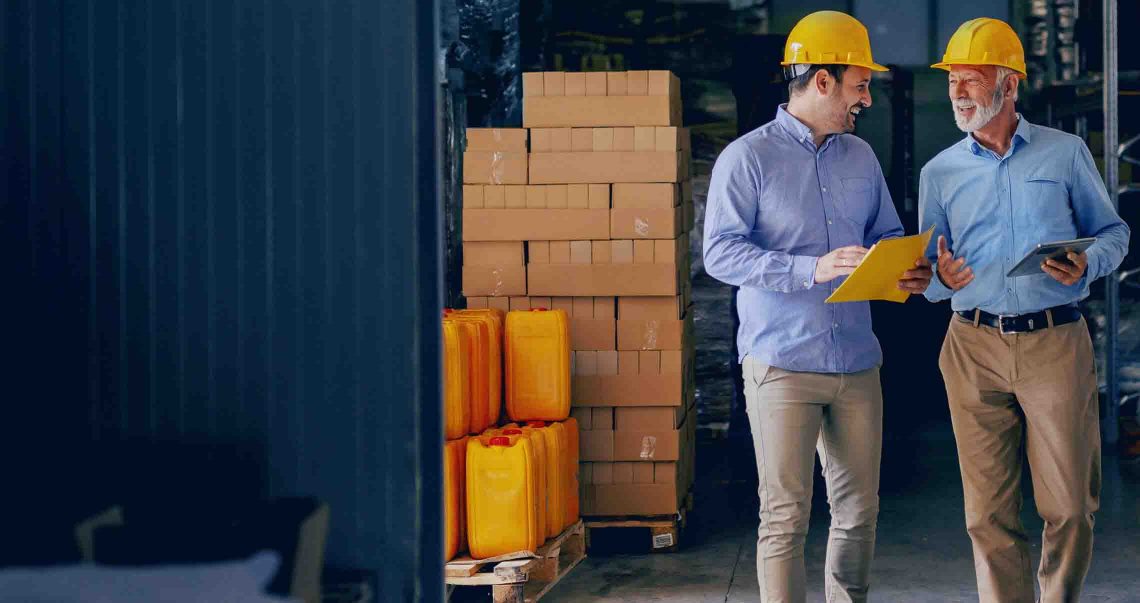
Staying competitive means embracing new developments while implementing the principles of risk management in manufacturing.
Plan for prevention
Risk management is more than just about safety—it's about taking control of the factors that drive profitability for your business. This is a continual effort, and it involves two main steps—identifying the risks, and mitigating them.
Managing risks doesn't always mean fully preventing them. Think of the process as getting prepared to minimize their impact on your business. The key is understanding the factors that make your operations profitable, as well as how any changes might impact your bottom line.
While the specific techniques you put in place to manage risk in your manufacturing company will be unique to your sector and your business, there are certain types of risk that are common across the industry.
Financial risks
Financial risks depend on the nature of business operations. Credit risk is the possibility that a client won't make expected payments in a timely manner. Interest rate risk is the likelihood that interest rates will go up, increasing variable loan payments and the cost of getting new credit to finance growth.
Meanwhile, currency risk emerges when fluctuations in a currency impact your ability to purchase supplies or sell finished goods. Manufacturers using a global supply chain can be particularly vulnerable to this type of risk. Even when your company conducts business in US dollars, your bottom line could be subject to currency risk if your supply chain heavily involves another currency.
Supply chain risk
Supply chains can be highly complex and continuously exposed to a variety of risks. Factors such as natural disasters, trade policy, political unrest and uneasy vendor relationships can create disruption. Any of these issues might lead to failure to meet client demand, resulting in loss of revenue, profit, market share and reputation.
The more visibility and control you have over your operations, the better you can respond to logistics and supply chain fraud issues in real time.
Cybersecurity
Like other industries, manufacturing has come to recognize the value of taking precautions against hacking, malware and other cybersecurity threats. It's important to stay vigilant even if your company's systems appear safe. Third-party vendors can expose your company to weaknesses and liabilities, particularly when vendors can access employee or customer information.
The Best Practices in Cyber Supply Chain Risk Management (PDF) from the National Institute of Standards and Technology outlines several risks and best practices protocols, including a checklist of questions to help keep manufacturers and distributors on the path to protection. Some cybersecurity questions manufacturers can ask themselves include:
- Is your vendor's software or hardware design process documented? Repeatable? Measurable?
- What controls are in place to manage and monitor production processes?
- What levels of malware protection and detection are performed?
- What type of employee background checks are conducted, and how frequently?
- How secure is the distribution process?
- How do vendors assure security through product life-cycles?
Labor risk
Do your operations depend on specialized labor? Does your staff often face the risk of major injuries while performing their jobs? Then labor may already be at the forefront of your risk management strategy.
Even if neither of these scenarios poses an issue for your company, it's still important to be mindful of employee-related risks. Hiring and training new employees can lead to unforeseen costs, and lawsuits can arise from general workplace issues or terminations.
According to the most recent data from the US Bureau of Labor Statistics, the reported rate of injury and illness was 3.2 for every 100 full-time workers in the manufacturing sector in 2022.
Best practices for risk management in manufacturing
Taking some strategic precautions and proactive measures can help you effectively mitigate risk in your organization.
Risk audits
First, it's a good idea to get a complete assessment of the ways your supply chain, finances and other key factors expose your organization to risk. A customized, comprehensive risk audit—performed either by a third-party vendor, or internally if you have the expertise and ability among your staff—can help you identify the information you need to understand where your biggest risks come from and how they change over time.
Data transparency and visibility
Using data to achieve supply chain visibility can help you maintain healthy partnerships and streamline operations, making it easier to pivot quickly in times of crisis.
It's key to eliminate information silos and outdated workflow practices, which can hinder access to critical data. Paper-based systems make it easy for documents to get lost or ignored. The only person who knows everything about a key process may be absent on the day you need them most. That golden spreadsheet with the critical calculations might carry an unnoticed data entry error for months.
Bolster your data security measures to protect your business and aid in fraud prevention. Data and document management software designed for manufacturers can help manage these risks. These tools bring together internal and external data to improve visibility across the supply chain, boost efficiency and make customer and vendor relations easier to manage.
Brace for financial risks
Put safeguards in place to help you manage the financial risks specific to your business. For example, you could maintain limitations on interest rates and customer debt exposure. You could also use automated alerts to stay informed of changes in currencies relevant to your operations.
Develop a risk management training program to help you and your employees self-regulate and address risk on a daily basis. Similarly, providing safety training and certifications for employees will help ensure mutual protection against injury and costly lawsuits.
Lastly, if you need help, a business banker or a trusted advisor can help you identify areas of risk you might be missing and implement strategies to mitigate them.